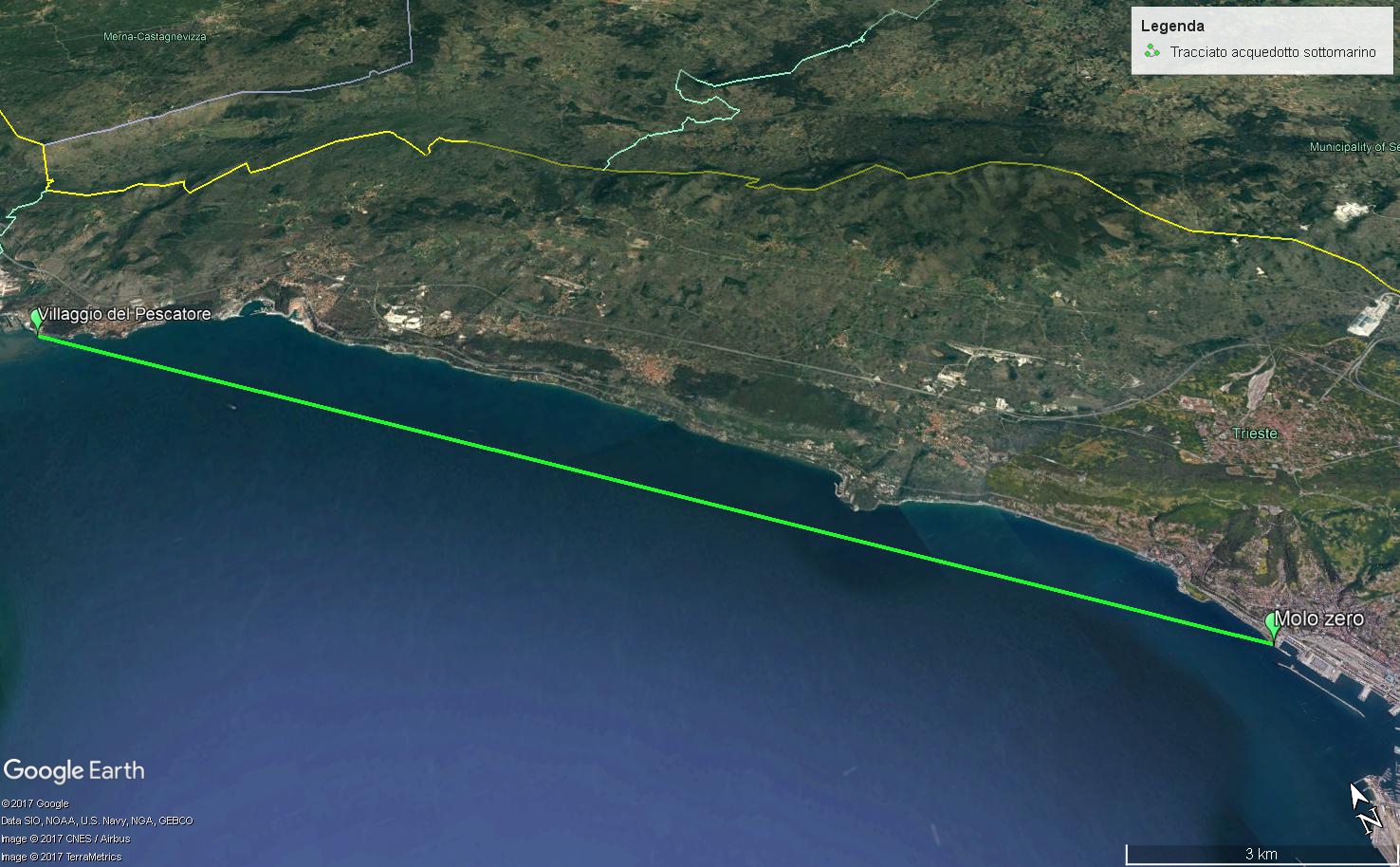
Photo: Layout of the Trieste transmission main (in green)
In collaboration with the Laboratory of Water Engineering of the Department of Civil and Environmental Engineering of the University of Perugia.
AcegasApsAmga SpA, of the Hera Group, manages the water systems of Padova and Trieste. Within the water supply system of Trieste, the submarine transmission main (TM) plays a crucial role. In fact it supplies not only the city of Trieste but also the Carsico plateau. Such an iron DN1330 pipe (Fig. 1) has a length of about 18 km and conveys 700 L/s with a steady-state pressure equal to 7 - 10 bars according to the elevation.
At present divers execute the inspection of the Trieste TM. With the aim of implementing a systematic inspection procedure, AcegasApsAmga SpA decided to proceed with a transient test-based technique (TTBT), which requires small pressure waves to be injected into the test pipe to detect anomalies. Particularly for submarine pipes, competitiveness and favorable prospects of TTBTs are undeniable with respect to other methods for a number of reasons. As an example, the short duration of the transient tests and the fact that only pressure measurements are needed are certainly in favor of TTBTs with respect to steady-state tests. The alternative option, i.e. the in-line type technologies with tethered and free-swimming sensors inserted into the pipelines, is more demanding from both the economic and logistic point of view. In fact such technologies imply the construction of quite expensive access points for the insertion and extraction of the sensors.
AcegasApsAmga SpA decided to call upon the expertise of the research group leaded by Bruno Brunone and Silvia Meniconi of the Water Engineering Laboratory (WEL) of the Dept. of Civil and Environmental Engineering of the University of Perugia (Italy) within an agreement between the University of Perugia and Ferrara. On behalf of AcegasApsAmga SpA activities are actively coordinated and controlled by Andrea Rubin, Lorenzo Tirello, and Pasquale Lucato.
Because of the large diameter, the installed valves cannot be closed as fast as required to generate small amplitude sharp pressure waves, which allow precise defect localization. As a consequence, the Portable Pressure Wave Maker (PPWM) device will be used (Fig. 2).
The PPWM and the Trieste transmission main during the tests
Such a device, refined at the Water Engineering Laboratory, has been awarded of the Sustainability prize within the 2016 H2O Bologna International Water Exhibition. It has been used successfully both in the laboratory and real pipe systems (as an example, the TM of Trento in Italy managed by Novareti SpA). The PPWM and test pipe are linked by a short conduit with a small-diameter connection valve at its end. Initially, the PPWM is brought to a higher pressure than that in the pipe. Opening of the connection valve causes a pressure wave that travels along the pipe detecting singularities.
Because of the importance of the Trieste TM, preliminary tests are in progress. Specifically, a numerical code has been refined to design the size and pressure of the PPWN and to simulate transient tests. Moreover, the flow-rate curve of the connection valve has been obtained by means of laboratory tests. Further preliminary tests will concern the analysis of the characteristics of the pressure waves generated by the PPWM.